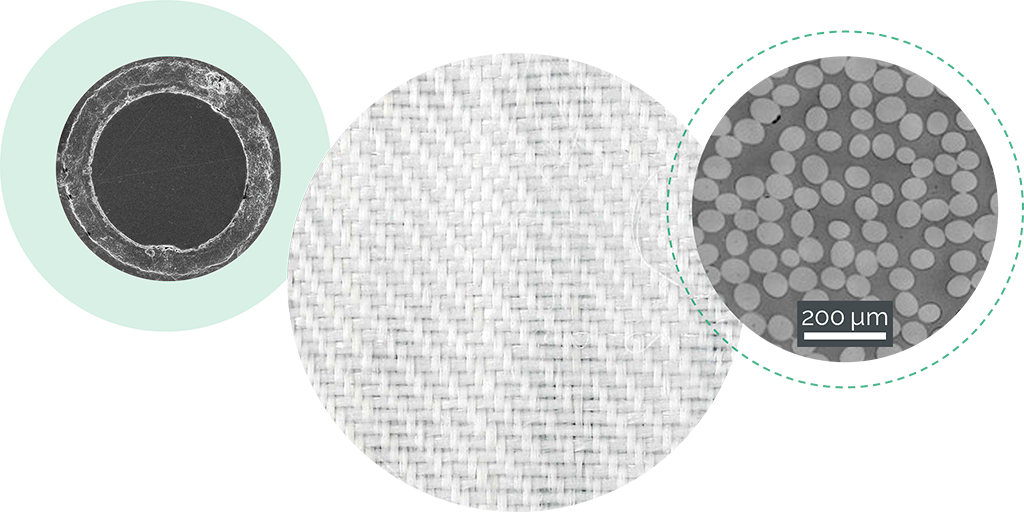
The benefits
Fibre-reinforced plastics for lightweighting.
The combination of stiff and strong reinforcement fibres and lightweight polymers makes fibre-reinforced plastics (FRP) the ideal material to reduce the energy demand of load-carrying structures.
The majority of reinforcement fibres used today are made from glass, because they offer the perfect trade-off between material cost, mechanical performance, and recyclability.
The challenging fit of materials and processes
Standard solutions are compromising on multiple levels in order to either enable the use of advantageous materials or to achieve low-cost processing.
The impregnation process
Today, continuous fibre-reinforced composites are mainly produced by impregnating dry fibre tows with the plastic in fluid form.
61% of FRP are produced with thermosetting resins that require chemical hardening through a curing process following the impregnation step.
These processes take time and energy and the resulting structures often include areas with poor material quality. So, a better solution providing more robust results is needed.
Thermoplastics for improved process performance
Around 40-50% of FRP contain thermoplastic matrix polymers. Compared to state of the art thermosets, thermoplastics offer a wide variety of benefits: The absence of time-consuming curing reactions, increased fracture toughness, the ability to weld, form and re-form, and the possibilities for repair, re-use and recycling.
The only issue: due to their high melt viscosity, standard impregnation is slow and expensive. That’s where Antefil’s hybrid fibre solution comes in.
Our award-winning solution in brief
Our technology was developed at ETH Zurich and filed as an award-winning patent protecting the way we produce our fibres, how they are converted into structures, and the fibre properties which enable these processes. Take a look at how this works yourself!
The choice of materials and processes also effects the footprint of composite structures. Find out more about the choices we’ve made.
Interested?
Discover what our technology can do for you.
Find out how you can get in touch with us.